Global Uranium Centrifuges Manufacturer Places Major Order for Oerlikon Leybold Vacuum’s Technology
Published on October 10, 2013 at 7:13 AM
http://www.azom.com/news.aspx?newsID=38569
Oerlikon Leybold Vacuum received a double-digit million Euro order for vacuum technology from a global manufacturer of uranium centrifuges for nuclear power facilities.
Oerlikon Leybold’s vacuum solutions will play an essential role in a nuclear plant presently under construction in the United States.
Oerlikon Leybold Vacuum will deliver proven fore vacuum equipment for
12 different systems and will offer customized service to fit the
customer’s needs, including assembly, testing and documentation in
accordance with requested standards. The RUVAC roots pumps have been
modified to withstand prevailing conditions and comply with the high
requirements of their application. “This order shows once again that we
are technological leaders in the mastering of highly complex and
demanding vacuum applications,” says Dr. Martin Füllenbach, CEO von
Oerlikon Leybold Vacuum.
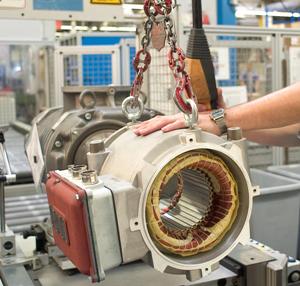
RUVAC Assembly
Uranium centrifuge technology is used not only in modern energy
solutions and civil power generation, but for medical and industrial
purposes as well. U-235 is the uranium isotope used in nuclear fission.
Nuclear reactors require a 4-5 % U-235 content for safe and efficient
operation, but natural uranium ore only has a 0.7 % U-235 content ratio.
The uranium for use in reactors must therefore be mined, milled and
converted to the appropriate gaseous chemical form, which allows those
molecules with higher amounts of U-235 to be selected out. This process
is known as uranium enrichment, and it requires the use of special
centrifuges. The process involves forcing pressurized uranium
hexafluoride gas through a series of porous membranes or diaphragms. As
U-235 molecules are lighter than U-238 molecules (a similar isotope that
exists alongside U-235), they move faster and have a slightly better
chance of passing through the pores in the membrane.
The UF6 that diffuses through the membrane has higher levels
of U-235, while the gas that did not pass through has depleted levels
of U-235. This process is repeated over and over in a series of
diffusion stages called a cascade. Each stage involves a compressor, a
diffuser and a heat exchanger to remove the heat of compression.
Finally, the enriched UF6 product is withdrawn from one end of the
cascade and the depleted UF6 is removed at the other end. The
gas must be processed through some 1,400 stages to obtain a product
with a concentration of 3 % to 4 % U-235. The plants typically achieve
only modest levels of isotope separation in each individual stage of
enrichment; they compensate for this by having the capacity to handle
large volumes of gas. The process requires a robust, stable vacuum.
“Our expertise does not end with vacuum components. An essential part
of this contract is vacuum engineering for process development. Given
our expertise and international reach, designing a system to the high
American specifications is business as usual”, says Segment CEO
Füllenbach. “Our understanding of customer needs, quality standards and
regulatory codes make Oerlikon Leybold Vacuum a trusted and reliable
partner and the supplier of choice.”
In light of the megatrends already discernible today, energy production
and transport will remain highly significant, especially for
innovations and technological developments relating to future energy
solutions.
Researchers Find Solution for Century-Old Chemistry Problem
Published on September 12, 2013 at 6:45 AM
http://www.azom.com/news.aspx?newsID=38232
Chemists at The Scripps Research Institute (TSRI) have found a way to apply a “foundational reaction” of organic chemistry to a stubborn class of chemicals, in a transformation that has been thought impossible for a century.
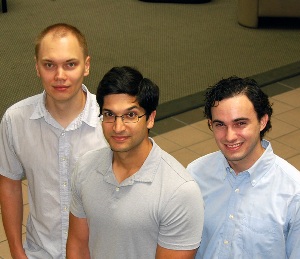
Authors
of the new Nature paper are TSRI Assistant Professor Ryan Shenvi
(center), Research Associate Sergey Pronin (left) and graduate student
Chris Reiher.
The classic SN2 reaction has enabled chemists to build and
modify many pharmaceuticals as well as other useful organic molecules.
While the reaction had been thought to exclude certain compounds, a
paper in the September 12, 2013 issue of the journal Nature describes a
new SN2-like reaction that overcomes this limitation.
“We’ve widened the range of molecules that are responsive to this
foundational technique; for example, we can now chemically synthesize a
family of promising antimalarial and anticancer compounds that were
previously off limits,” said TSRI Assistant Professor Ryan A. Shenvi,
who was the senior author of the paper.
Flipping the Umbrella
The SN2 reaction can be used to detach part of a molecule
called a functional group from a central carbon atom, while
simultaneously, another functional group adds to the opposite side of
the carbon atom. This structural flip can significantly change a
compound’s chemical properties.
“It’s like turning an umbrella inside out,” Shenvi said. “The SN2 predictably inverts what we call the stereochemistry of the carbon atom.”
Traditionally, stereoinversion reactions, which were first described by
Paul Walden in 1896, have not been applicable to compounds known as
tertiary alcohols or their derivatives—a general problem identified by
Christopher Ingold in the early 1900s. In these compounds, the carbon
atom of interest is bonded to three other carbon atoms, which
effectively shield it from the reaction.
To get around this longstanding limitation, Shenvi and his research
associate Sergey V. Pronin developed a method that employs a special
acid catalyst plus an unusual nitrogen-containing molecule, a derivative
of cyanide. The acid helps detach a fluorous functional group from one
side of the central carbon atom, and then the nitrogen forms a new bond
on the other side, thus completing the stereoinversion.
“The basic idea is that you can take a tertiary alcohol with one
stereochemical configuration and install nitrogen functionality, leaving
it with the opposite stereochemical configuration,” said Pronin.
Fewer Steps
To demonstrate the new technique, Pronin and graduate student Chris
Reiher used it to build or modify a number of compounds in a relatively
short sequence of reaction steps, starting with cheaply available
tertiary alcohols. “In one example, we took a derivative of vitamin E,
tocopherol, and in a few steps turned it into something we call an
aza-tocopherol, in which the oxygen atom is replaced with nitrogen—a
compound that otherwise would have been very difficult to access,”
Pronin said.
The chemists also showed how the new reaction can simplify the
preparation of a set of compounds known as marine isocyanoterpenes,
which are produced naturally by sea sponges and other oceanic animals.
Some of these compounds have been found to have anticancer,
antimalarial, antifungal and other potentially useful properties, but
they have been very hard to prepare using synthetic chemistry. With the
new technique, the researchers were able to prepare several scarce
marine isocyanoterpenes starting from abundant and renewable terrestrial
terpenes, and using far fewer steps than had ever been reported before.
On its own, the new method fills a significant gap in the toolkit of
organic chemists. But Shenvi hopes soon to extend it further to enable SN2-like
substitutions of tertiary alcohols with other reaction partners: “We
think that this reaction will teach us how to achieve stereoinversions
of tertiary carbons to form carbon-oxygen, carbon-sulfur and even
carbon-carbon bonds,” he said.
This year would have been Paul Walden’s 150th birthday.
Funding for the research was provided in part by Eli Lilly and Boehringer Ingelheim.
About The Scripps Research Institute
The Scripps Research Institute (TSRI) is one of the world's largest
independent, not-for-profit organizations focusing on research in the
biomedical sciences. TSRI is internationally recognized for its
contributions to science and health, including its role in laying the
foundation for new treatments for cancer, rheumatoid arthritis,
hemophilia, and other diseases. An institution that evolved from the
Scripps Metabolic Clinic founded by philanthropist Ellen Browning
Scripps in 1924, the institute now employs about 3,000 people on its
campuses in La Jolla, CA, and Jupiter, FL, where its renowned
scientists—including three Nobel laureates—work toward their next
discoveries. The institute's graduate program, which awards PhD degrees
in biology and chemistry, ranks among the top ten of its kind in the
nation. For more information, see scripps.edu.
Source: http://www.scripps.edu
Tell Us What You Think
Do you have a review, update or anything you would like to add to this news story?
POWER AND INCINERATION INDUSTRY
Power
Refractory technology for this industry has changed with the evolution of new demands for power and economic and environmental concerns. A wide variety of materials are available for use in industrial boilers, package boilers, cyclone boilers, waste-to-energy units, CFB''s, ash hoppers and others.
Boiler Refractory Applications
Power Generation
Ash Hopper Refractories
Incineration
Boiler Refractory Applications
Penthouse |
![]() |
Special Applications |
|
Furnace Walls |
|
Ducts | |
Burners | |
Ash Hopper |
Burners | Tangential and Front Fired | |
Special Applications | Slagging Bottom Boiler | |
Cyclone Boiler Studded Tubes |
||
Baffles and Boiler Seals | ||
Floors (Industrial Boilers) | ||
Stoker Pier (Industrial Boilers) | ||
Hearth (Recovery Boilers) |
BACK TO TOP
Power Generation
The correct selection of refractory for CFB''s can prolong service life and improve overall operational efficiency. ANH has been a preferred refractory supplier to the Power Industry for over 50 years.
H-W product families offer a complete package of solutions for all service conditions:
|
![]() |
Fuel Feed Systems | Service Conditions:
|
Lining Solution: |
Combustor |
Service Conditions:
|
Lining Solution: |
Crossover duct |
Service Conditions:
|
Lining Solution: |
Cyclones |
Service Conditions:
|
Lining Solution: |
Ash Return Systems |
Service Conditions:
|
Lining Soulution: |
Outlet Ducts / External Heat Exchangers Ash Coolers |
Service conditions:
|
Lining Solution: |
BACK TO TOP
Ash Hopper Refractories
Ash-Hopper Service
Ash
hopper service includes a number of conditions, which can be
detrimental to a refractory lining. Refractories used in this service
must show good resistance to a variety of destructive conditions.
|
![]() |
Tufshot LI | Service Classification - Less Severe |
Installation Method - Gun Impact Resistance - Good Thermal Shock Resistance - Fair Abrasion Resistance - Fair |
Tufcast LI | Service Classification - Less severe |
Installation Method - Cast Impact Resistance - Good Thermal Shock Resistance - Fair Abrasion Resistance - Fair |
Lo-Abrade G | Service Classification - Severe |
Installation Method - Gun Impact Resistance - Excellent Thermal Shock Resistance - Good Abrasion Resistance - Good |
Versaflow 45 Plus | Service Classification - Severe |
Installation Method - Cast Impact Resistance - Excellent Thermal Shock Resistance - Fair Abrasion Resistance - Good |
Versaflow Thermax Plus | Service Classification - Most Severe |
Installation Method - Cast Impact Resistance - Excellent Thermal Shock Resistance - Excellent Abrasion Resistance - Excellent |
Versagun Thermax Adtech | Service Classification - Most Severe |
Installation Method - Gun Impact Resistance - Excellent Thermal Shock Resistance - Excellent Abrasion Resistance - Good |
Greentec 170 LG | Service Classification - Most Severe |
Installation Method - L.C Gun Impact Resistance - Excellent Thermal Shock Resistance - Good Abrasion Resistance - Excellent |
Incineration
Incineration of corrosive waste has become an increasingly acceptable method of disposal for these materials. Commercially and privately operated incinerators will be a part of the foreseeable future. Conditions relative to refractory longevity vary throughout these units. Careful selection of refractory materials is required to achieve long running campaigns and maximise cost effectivness. Thermal profiles, waste streams, generated slag and operating practices are individual for each incinerator in operation. Therefore refractory practice is an individual matter.
Incinerators are used to destroy -
- Liquids / Sludge / Solids / Gases
- Temperature - 900 to 1450°C
- Abrasion - solids, metals, gas streams
- Chemical - sulphur, chlorine, organics
- Slags - ashes, metals, phosphates, chemical
- Gases - organics, chemicals
- Mechanical - metal drums, slags
- Medical - hospitals, pharmaceuticals
- Industrial - tyres, inks, packaging
- Cremation - local authorities, veterinary
- Sewerage - water companies
- Municipal - town refuse
- Agriculture - animals, soils
- Government - money, military, drugs, documents
- Chemical - dangerous toxic wastes, petrochemicals
- Power Gen - heat recovery systems
- Marine - shipboard wastes
- Municipal - moving/rotary grate, CHP
- Fluid bed - circulating, bubbling
- Rotary - chemicals, solids, liquids
- Multi Hearth - sewerage
- Modular - medical, solids
- Cremators
- Waste Boiler - paper, oils, sugar cane
- Waste Gas - flare stacks
- Thermal Oxidisers
- Coal/Oil Gasifiers
- Spent Caustic Incinerators
Tidak ada komentar:
Posting Komentar